Do You Have An Engineering Project We Can Help With?
Design
Our engineers have a strong stress background that results in more efficient product design. This allows for a complete solution for virtual and rapid prototyping, testing, and low rate initial production. Component design encompasses material selection with profile optimized for load paths, failure modes, and sustainability. Full 2D and 3D drawing packages with stress reports are produced to meet your requirements.
- Generate 3D drawings from legacy 2D drawings
- 3D drawings for modifications such as antennas, racks, or repairs
- Concurrent design and analysis to optimize results
- Variety of drawing formats to meet customer requirements
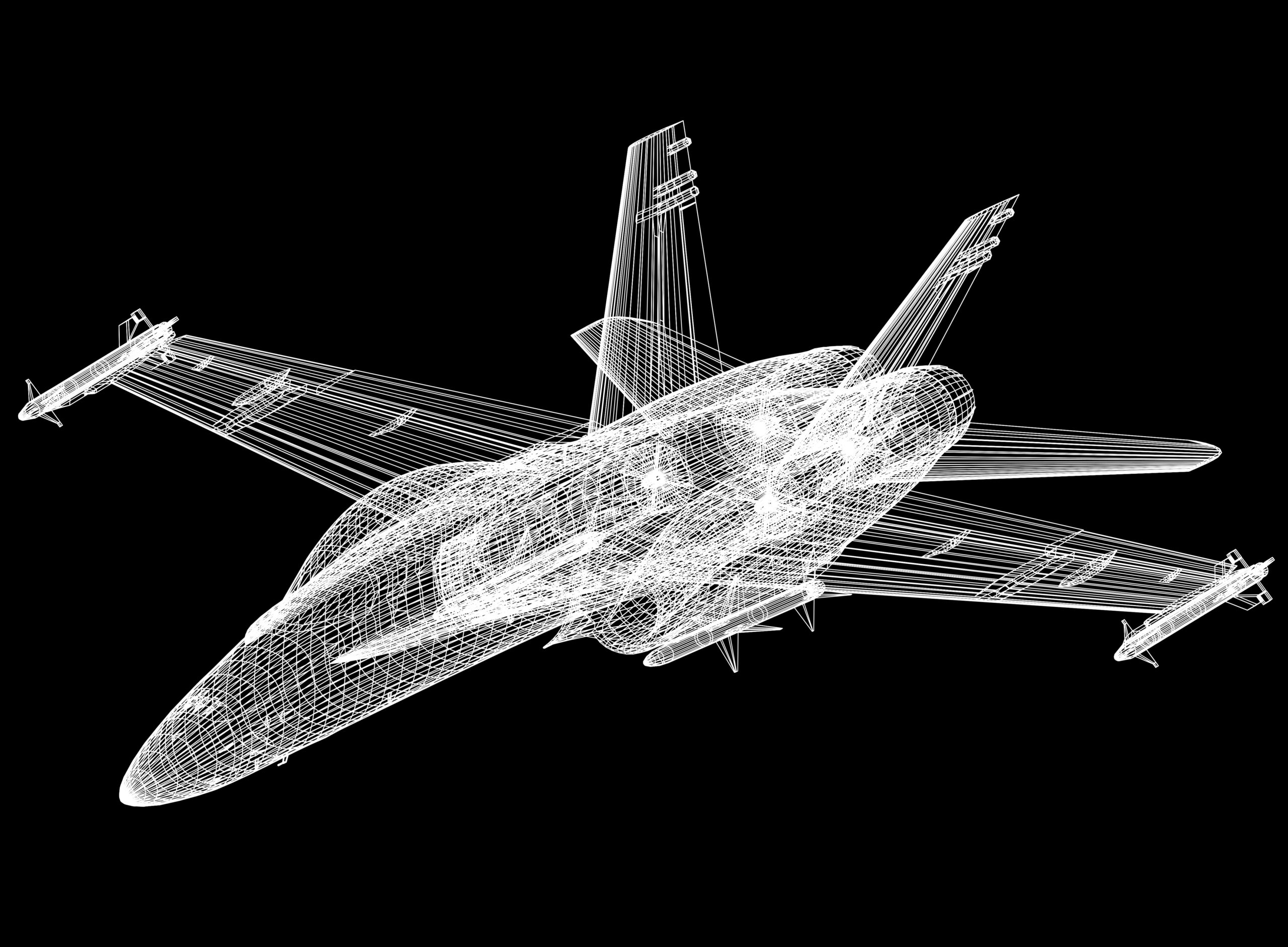
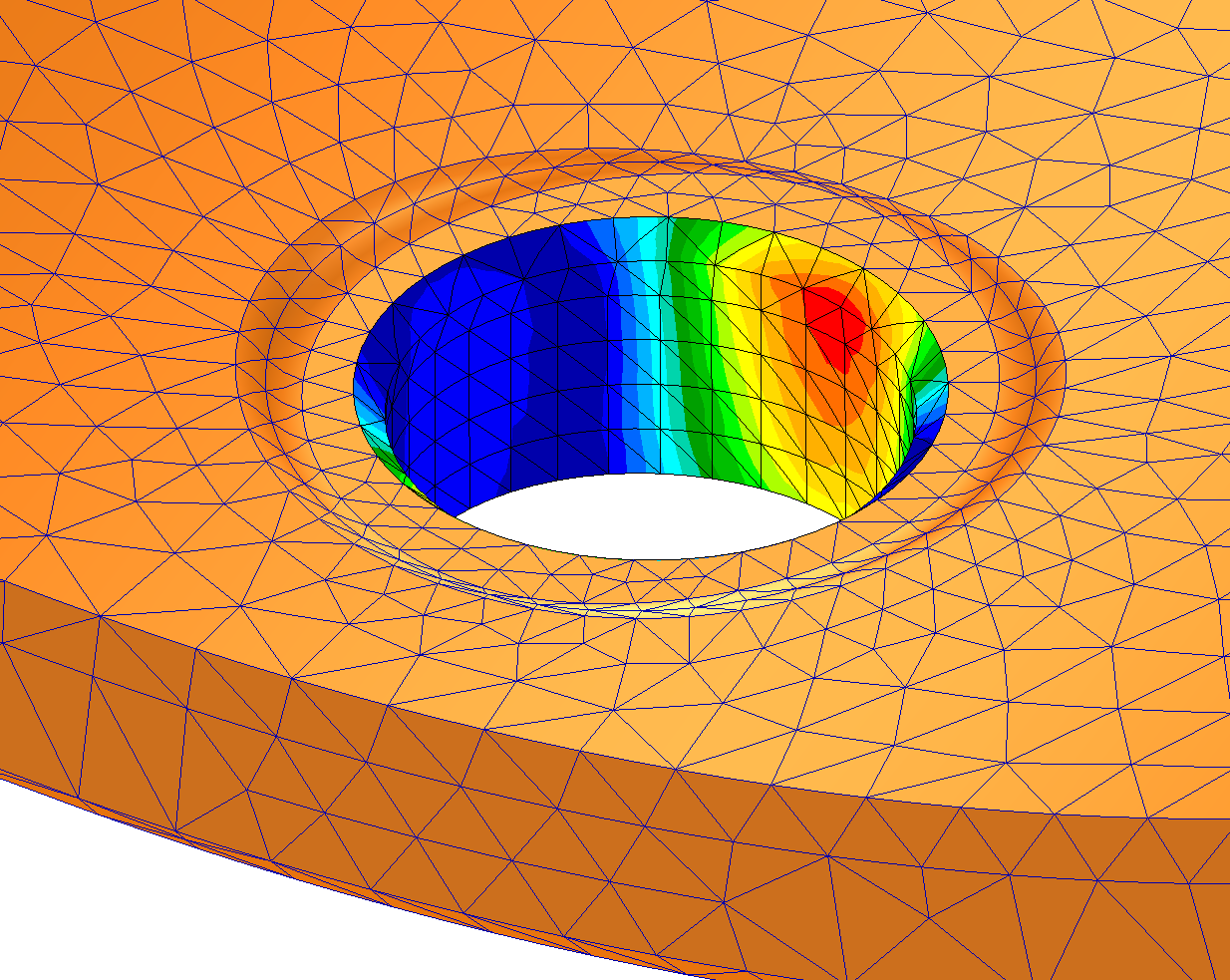
Analysis
Structural analysis is the foundation of our services. Our primary goal is to provide safe, fast, effective, results. From classical to advanced finite element analysis, KAES can tackle any challenge to deliver the most effective solutions for your problems.
- Classical analysis for all ultimate (static) load conditions for tension, compression failure modes
- Peak stress determinations using finite element or classical methods to support fatigue analysis
- Crack initiation life and crack growth analysis using strain and/or stress based methodologies
- Finite element modeling – air vehicle internal loads models, 3D multibody contact models, linear and nonlinear, modal, dynamics
Programming
Automated tools can be created to significantly increase the efficiency of your engineering staff. These tools automate repetitive tasks performed and facilitate consistent results.
- Tools can be created in various software packages to meet your needs such as VBA, Python, C++, HTML.
- Web based interface for easy access and security.
- Integrate machine learning to automatically build databases and predict results.
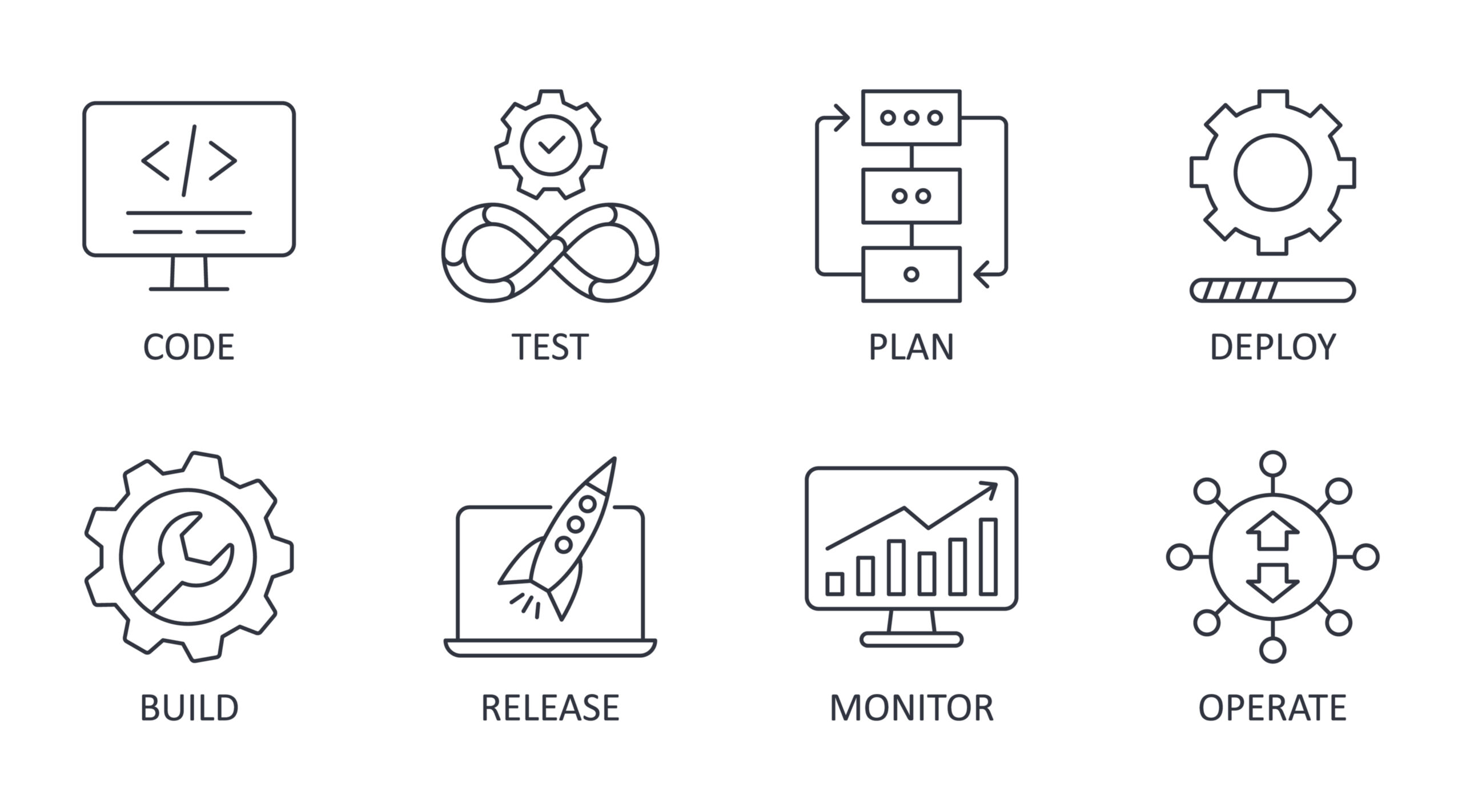
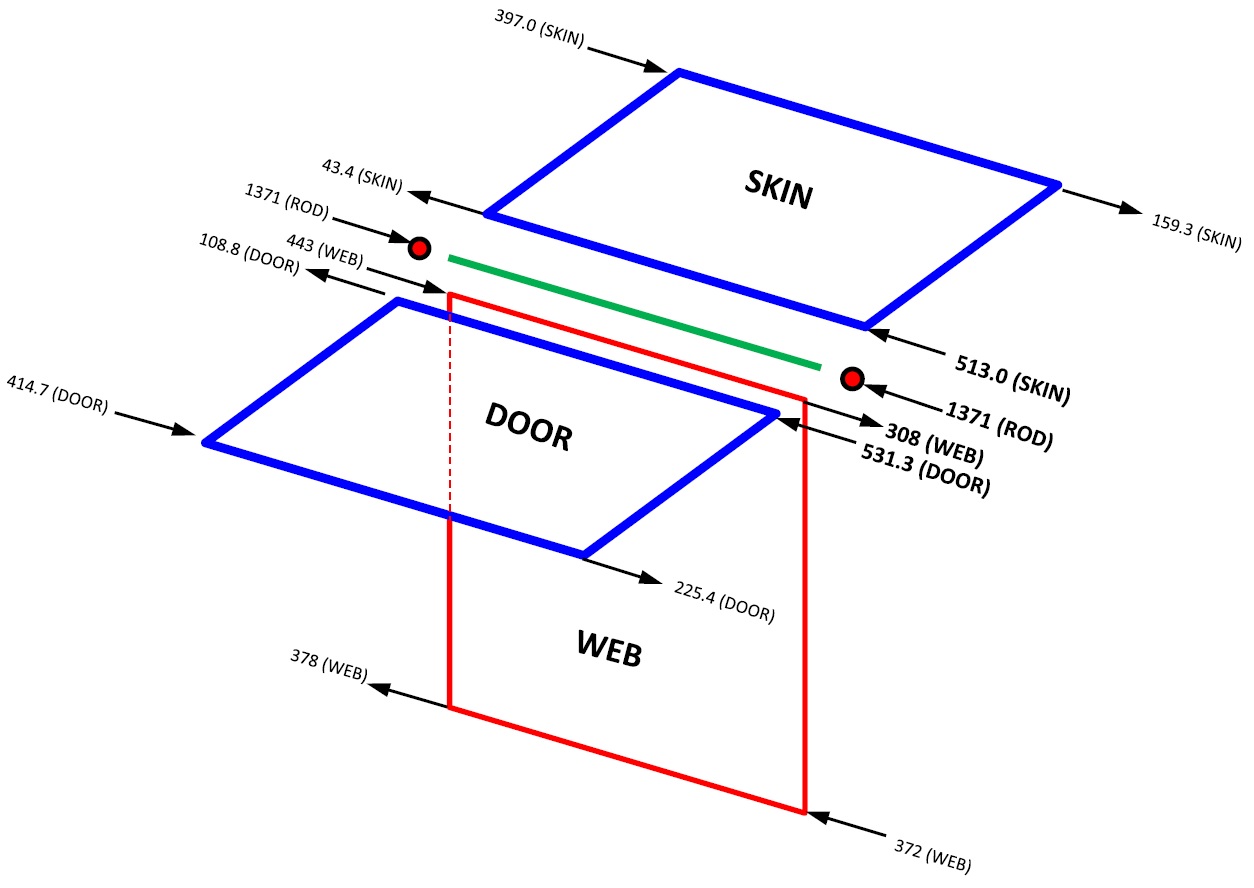
Training
Practical Aerospace Finite Element Model Interpretation and Load Derivation
This practical finite element course focuses on optimizing internal loads development procedures among other concepts. The course also provides comprehensive practical finite element modeling procedures, tips and guidance to properly idealize and de-idealize the structure. Aircraft platform stress analysis samples are used in the course to demonstrate the load derivations. The course is 32 hours and typically broken into a 2 day lecture followed by a 2 day workshop solving real world problems.